De la physique au pharmaceutique : Les origines du DPTE® original
Membre de Getinge depuis 2005, La Calhène est pionnière dans la technologie de confinement et de transfert aseptique depuis près de six décennies.
Aujourd’hui, nous sommes tous conscients de l’importance de protéger les personnes des rayonnements. Cependant, ce n’est qu’à l’aube de l’ère nucléaire des années 1940, près d’un demi-siècle après la découverte des rayons X par Wilhelm Roentgen, que nous avons commencé à comprendre les effets mortels des matières radioactives. Alors que les chercheurs et les ingénieurs recherchaient des moyens de garantir la sécurité des personnes, leur priorité absolue était de créer une solution de confinement avec un joint parfaitement étanche.
Dans les années 1960, La Calhène a commencé à travailler avec le Commissariat à l’énergie atomique et aux énergies alternatives (CEA) pour développer des systèmes de manutention à distance ainsi que des conteneurs spéciaux pour les déchets radioactifs. Ensemble, ils ont également co-breveté le premier système de confinement mécanique au monde : DPTE® qui signifie « Double Porte de Transfert Étanche ». Il est connu sous le nom de port de transfert rapide.
Pour créer un joint parfaitement étanche, le système DPTE® comporte deux parties : une porte Alpha et un conteneur bêta ou un sac souple (DPTE-BetaBag®). La porte Alpha est installée sur la paroi d’un système de barrière et comprend une bride, un joint et une porte. L’arrimage et la rotation à 60 degrés de la partie bêta créent une connexion sécurisée à un conteneur, un autre isolateur ou un dispositif approprié pour les transferts tel qu’un sac.
Depuis 30 ans, La Calhène est le seul fabricant de ce type de port étanche avec verrou sécurisé qui élimine les erreurs humaines. Ils ont également été les premiers à se rendre compte que le système DPTE® pouvait être adapté pour une utilisation dans d’autres secteurs où la protection est cruciale.
DPTE® dans l’industrie pharmaceutique
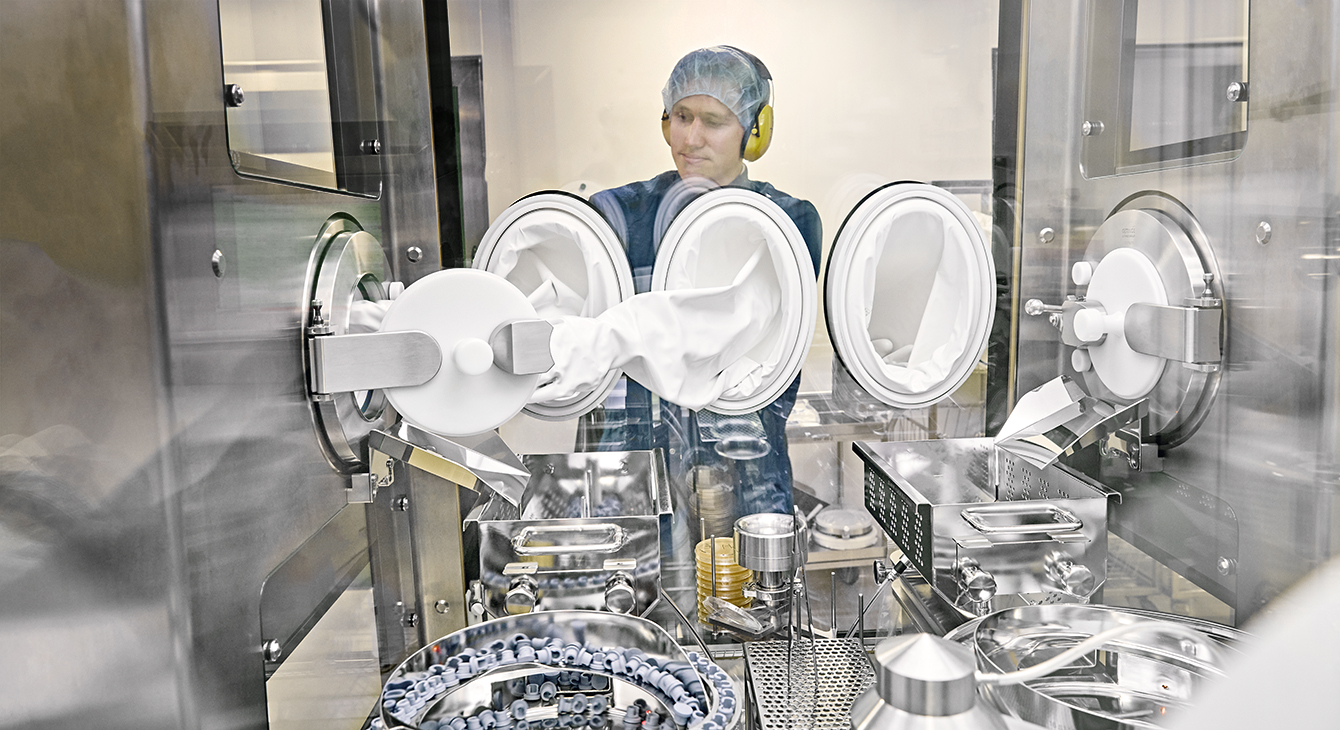
Le concept de protection du monde extérieur contre la contamination a entraîné une révolution dans la production de médicaments injectables. Dans la fabrication de produits pharmaceutiques, la technologie pouvait être utilisée dans une perspective opposée : protéger les patients en protégeant les matériaux à l’intérieur du système de barrière.
Les solutions de confinement ont été une innovation essentielle dans la recherche et la médecine. Au fur et à mesure du développement de nouvelles technologies – des boîtes à gants dans les années 1930 aux filtres HEPA après la Seconde Guerre mondiale – a commencé à prendre forme la salle blanche que nous connaissons aujourd’hui. Cependant, les opérateurs ont toujours été confrontés à un défi majeur : comment transférer des matériaux dans et hors de l’environnement « stérile » de l’isolateur de traitement aseptique sans rompre la stérilité.
Dans les années 1940, les isolateurs étaient fabriqués en acier inoxydable avec de petites fenêtres et étaient reliés à un petit autoclave. L’installation était coûteuse et peu pratique. En 1978, La Calhène a mis au point la première unité de fabrication pharmaceutique au sein d’un système d’isolateur pour une société italienne biopharmaceutique. Cette unité de remplissage de poudre a été l’une des premières à utiliser le DPTE® en dehors de l’industrie nucléaire.
Au milieu des années 1990, la conception des lignes de remplissage a été modifiée pour s’adapter au DPTE®. Auparavant, les lignes étaient placées dans des salles blanches de classe ISO 5, mais en les adaptant aux isolateurs, on a créé un système fermé avec le DPTE® qui assure une protection totale du produit lors du processus de stérilisation ainsi que des personnes dans l’environnement.
Des solutions à usage unique innovantes
Aujourd’hui, l’innovation du DPTE® continue d’améliorer la sécurité des patients en réduisant le risque de contamination grâce au DPTE-BetaBag® à usage unique et prêt à l’emploi. Favorisant une efficacité et une sécurité accrues dans de nombreuses applications, la gamme DPTE-BetaBag® est fabriquée dans un environnement ultra-propre (ISO 7 et ISO 5) et peut être pré-stérilisée et même fournie pré-remplie avec des composants de fabricants, éliminant ainsi le besoin de faire appel à des services de traitement spécial.
Développés pour permettre un débit élevé continu sur une longue ligne de remplissage stérile de produits ophtalmiques pour MSD (Merck France) en 1994, les sacs souples sont connectés aux portes Alpha DPTE® afin de fournir un approvisionnement sécurisé en composants stérilisés. La question de savoir comment stériliser et insérer des composants en plastique dans une ligne de remplissage aseptique à haute vitesse a été résolue en insérant les éléments dans un DPTE-BetaBag®, qui est ensuite stérilisé aux rayons gamma avant d’arriver dans la salle de production. Le système DPTE® garantit un transfert sûr et étanche sans perte de confinement.
Tout cela constitue un héritage incroyable sur lequel Getinge s’appuie en permanence, garantissant ainsi à ses clients une production flexible, optimisée et rentable, ainsi qu’un niveau élevé de sécurité des processus et des patients.
En savoir plus sur le DPTE® original et les autres solutions d’isolation et de transfert stérile de Getinge.