Efficient sterilization in production of heat sensitive goods
- Safe, reliable, and repeatable results
- Protect the integrity of products and packaging
- Faster sterilization process
The unique properties of ethylene oxide (EO) make it suitable for the sterilization of products that are sensitive to heat and humidity. EO can penetrate wrapped and packaged goods to effectively sterilize at very low temperatures, making it the ideal technology for low-temperature terminal sterilization.
Getinge supports you with optimizing a complete EO sterilization plan for your specific product, workflow, and facility layout.
Watch the video to discover the GEE Ethylene Oxide Sterilizer on an EtO sterilization plant.
Process control
Control system
The GEE Ethylene Oxide Sterilizers are equipped with a PLC automation (Allen Bradley or Siemens) system and is usually connected to a central supervisory control and data acquisition (SCADA) system for overall process monitoring and control. The system provides audible and visual notification in event of deviation from the operating parameters. The PLC can be configured for specific process requirements allowing for optimization of your processes while protecting the product packaging by controlled pressure ramping. Data storage, format and monitoring are fully flexible to support specific process needs.
SCADA
The HMI interface is built on a full SCADA system that is 21CFRPart11 compliant. The system includes multiple screens for process viewing and system operations. Built-in traceability functions ensure all processes, machines, and pallets are registered and documented throughout the process.
Batch reporting features include both detailed and summarized reports as well as auto batch release functions.
Safety
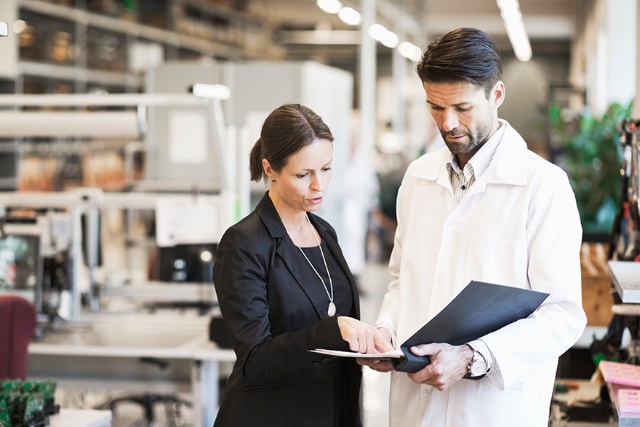
Safe production processes
The safety of your staff is of paramount importance.
The GEE Ethylene Oxide Sterilizers are built for full compliance with ATEX regulations and all designs are subject to risk and failure analysis techniques (HAZOP, FMEA).
Our systems include redundant safety features to give you peace of mind over your process.
Control of the EO
A built-in automatic chamber leak rate test also tests the integrity of the EO supply line from the gas room to the chamber as part of every cycle. The EO is vaporized by gas dispensing equipment located outside the building, which prevents liquid EO from entering the facility. The dual door gasket assures that EO cannot leak out of the chamber when in positive pressure, and that air cannot leak into the chamber when in negative pressure.
Process safety through PLC and SCADA
The PLC activates alarms when the process is outside normal operating parameters and reacts accordingly with appropriate steps. With the SCADA operator control station option, sophisticated software calculates if the cycle will operate within the flammability curve and automatically informs the operator if the programmed cycle has a flammable mix. It can also be set-up to inhibit cycle start, if required.
Leak-tight door design
When closed, the door is sealed using a dual gasket system that will remain leak tight even if all services fail. The door is automatically sealed by pushing the two door seals against the door face using pressurized nitrogen. A pressure switch monitors the pressure behind the seal. In the event of a loss of nitrogen, a high-pressure tank will back up the door seal until the sterilizer can complete a process to safe cycle end.
Load handling
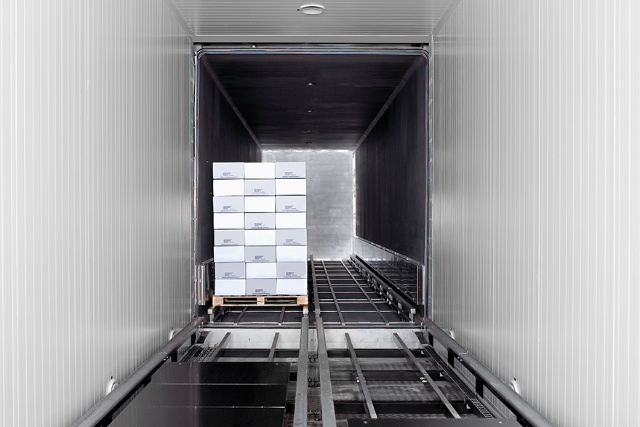
Safe and efficient load handling
Getinge’s automatic pallet transfer system (APTS) is a safe pallet lift and movement system that can transfer single or multiple pallets in two linear directions for automatic loading of the products.
Pallets are accurately positioned within the chamber to maximize throughput and efficacy. The system has no moving parts within the sterilizer chamber and requires no operator entry into the EO chamber, making it a safe solution.
Movements using pneumatic motors and components allow for system operation in ATEX-classified environments.
Process outline
The EO sterilization process consists of three stages. These stages can be performed within the sterilizer chamber or in three separate chambers.
Pre-treatment
In the pre-treatment stage the load is heated and humidified to prepare for sterilization.
EO sterilization
The load is sterilized with the correct concentration of EO gas at low temperatures.
Post-conditioning/degassing
In the post-conditioning stage, the gas is removed from the product and packaging for safe downstream handling.
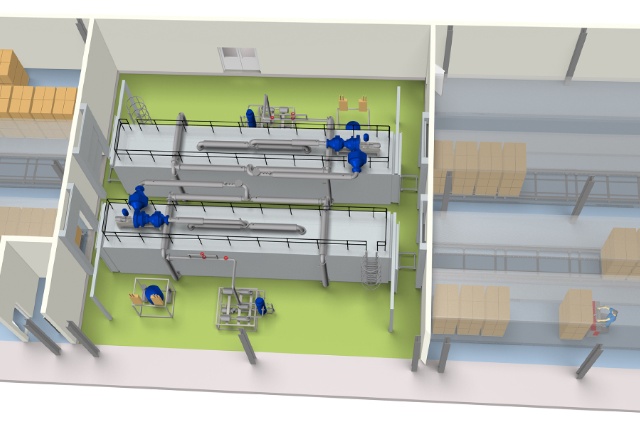
Temperature control
To ensure rapid heating and a consistent load temperature, heated water is circulated through the jacket and doors. If required, a cooling system can also be included for rapid transition to lower temperatures.
Chamber recirculation
The chamber recirculation system is essential to ensure uniform gas and temperature distribution. The external distribution piping is heated to maintain temperature and minimize losses.
Vacuum system
GEE EO Sterilizers are equipped with liquid ring vacuum pumps providing efficient air removal of sterilizer chamber and internal load. The vacuum system removes high concentrations of EO from the chamber in a short period of time.
Gas dispensing
EO is usually supplied as liquid in pressurized containers. Vaporization ensures that liquid EO does not enter the sterilization area. The heating medium can be either steam or hot water for accurate temperature control and flow regulation.