Real Small... Real Bioreactors
- Easy set up and operation
- Little bench space required
- Less medium used during cultivation
- Generate more data in less time
The Applikon Bioreactors are your ideal devices for small-scale operations in the lab. They save time, take up less bench space, and generate more data while providing fully scalable results. In combination with our highly efficient BioSep cell separation device, you can convert your batch or fed-batch bioreactor into a small scale continuous bioprocessing system.
The configurable head plate of the bioreactor has Luer fittings that free up space for multiple additions, sensors and fittings and ready-to-go tubing assemblies for a quick start.
Microbial and cell cultures at small scale
Sometimes less leads to more.
The Applikon Bioreactors require less medium and bench space than regular laboratory-scale bioreactors. Scientists can easily run multiple experiments in parallel, generating more data at once to enable efficient scale-up.
Watch the video to view how the Applikon Bioreactors can speed up your bioprocess.
Related Content
Articles
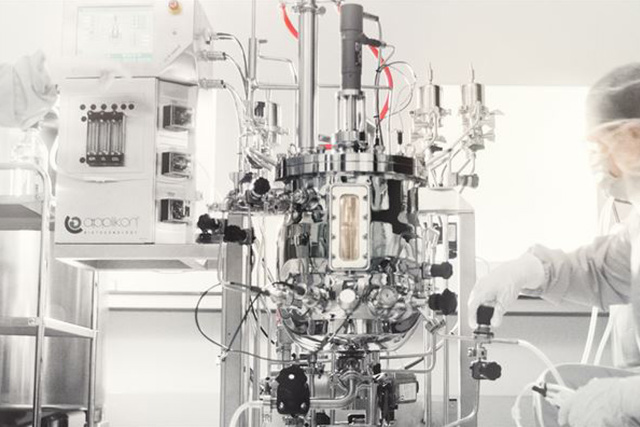
Getinge’s bioreactors to support unique Dutch cellular agriculture initiative
The Dutch government confirms the allocation of €60 million to support an ecosystem around cellular agriculture, the technology used to produce animal products such as meat and milk proteins directly from animal and microbial cells. As a member of the Cellular Agriculture Netherlands Foundation, Getinge will support the project with its bioreactors and bioreactor knowledge.
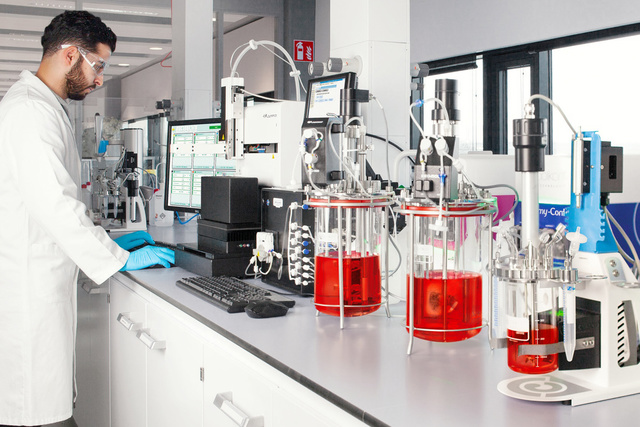
Bioreactors pave the way for eating seafood without fishing
Recently, Bluu Seafood in Germany presented their first market-ready products made from cultivated fish cells – a milestone in enabling people to eat seafood without compromising animal welfare or straining marine ecosystems. Instead, the cells used to make fish fingers and fish balls are growing in bioreactors supplied by Getinge.
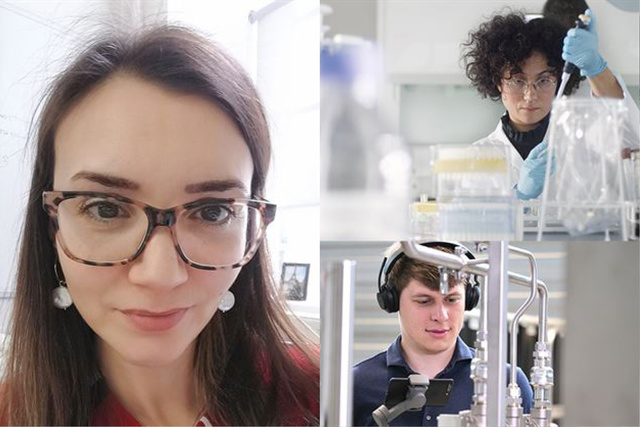
Bioreactors to help grow cellular agriculture
Though the global population is expected to reach 10 billion in 2050, resources to feed everyone are limited. One way to help solve the challenge is the revolution of Cellular Agriculture, an area where Getinge’s bioreactors can play an important role.
On Demand Webinars
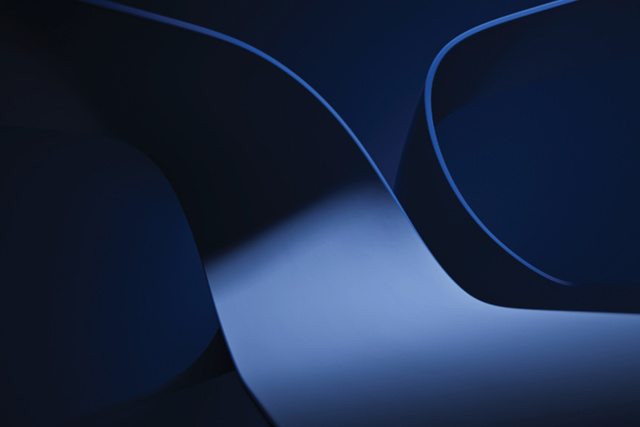
Cellular Agriculture - The Future of Food
by Imko Gaastra - Product Manager, Getinge Life Science & Dr. Mariana Petronela Hanga - Lecturer Biochemical Engineering, UCL
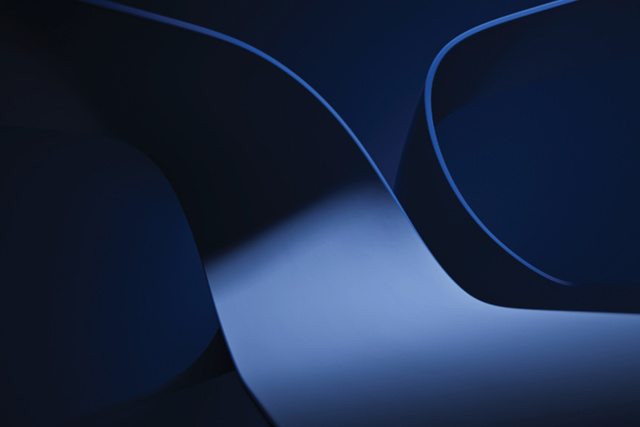
GMP Biomanufacturing Solutions
Walk the Halls of Getinge Applikon following a Stainless Steel Project
Small size bioreactors
The compact design of the Applikon Bioreactor allows the scientist to place multiple systems on the valuable bench space. Parallel processing has never been that easy.
Generate scalable results
Running cultivations at small scale allows for quick access to more data. Scientists will have reliable data that simplifies scale-up to higher volumes.
Specifications
Applikon Bioreactor 250 |
Applikon Bioreactor
|
Applikon Bioreactor
|
|
Total volume (mL) | 290 | 550 | 1250 |
Working volume (mL) | 200 | 400 | 1000 |
Minimum working volume (mL) | 50 | 100 | 200 |
Aspect ratio total volume | 2.3 | 2.1 | 2.3 |
Aspect ratio working volume | 1.6 | 1.5 | 1.9 |
Dimensions (dxh) | 180 x 400 mm | 195 x 400 mm | 200 x 550 mm |
Dimensions for autoclaving (dxh) | 180 x 250 mm | 195 x 250 mm | 200 x 400 mm |
Drive system | Direct drive, lipsealed | Direct drive, lipsealed | Direct drive, lipsealed |
Maximum stirrer speed (rpm) | 50 - 2000 | 50 - 2000 | 50 - 1750 |
Maximum impeller tip speed (m/s) | 2.3 | 2.9 | 3.5 |
Impellers | Choice of Rushton and Marine | ||
Gas sparger | Porous sparger, open pipe sparger or jet sparger | ||
Gas overlay | Yes | ||
Exhaust gas | Electrically cooled exhaust gas condenser (evaporation <4% per day at 37°C @ 2vvm) | ||
Sampling | Fixed sample pipe with optional sampling system | ||
Draining | Height adjustable drain pipe | ||
Additions | 4 fixed inlet ports and optional micro liquid injectors | ||
pH | Measurement: 8 mm classic pH sensor Control: via acid pump (variable speed pump) or CO2 gas in combination with alkali pump (variable speed pump) |
||
DO2 | Measurement: LumiSens Optical DO2 sensor. Control: via a combination of N2, Air, O2 (needle valve standard, MFC optional) and agitation |
||
Temperature | Measurement: Pt-100 sensor in thermowell in topplate Control: electrical cooling and heating jacket via bioreactor wall |
||
Foam | Measurement: Height adjustable conductivity based foam sensor Control: anti-foam addition (variable speed pump) |
||
Level | Measurement: Height adjustable conductivity based level sensor Control: variable speed pump for liquid addition or removal |
||
Optional inlets | Septum, chemostat tube, liquid entry system | ||
Optional sensors | Biomass, Optical Density, O2 and CO2 off gas, weight balance |
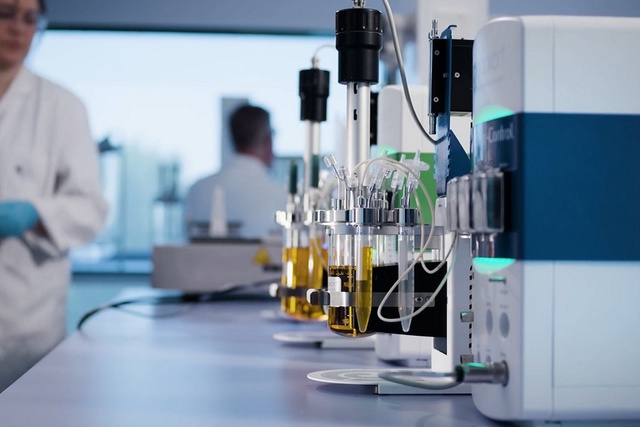
The Applikon Bioreactor is ideal for the following applications:
- Screening studies
- Media optimisation
- Process optimisation
- Microbial and cell culture
- Batch, Fed-Batch, Perfusion and Continuous cultivation